Ключовата разлика между PFMEA и DFMEA е, че PFMEA помага да се анализират потенциални неуспехи на определен процес на бизнес единица, докато DFMEA помага да се анализират потенциални неуспехи на дизайн на продукт.
Методът на FMEA (Анализ на ефектите от режима на повреда) помага да се идентифицират потенциални режими на повреда на процес при управление на операциите и дизайн на етапа на разработване на продукта в рамките на системата и да се категоризират повредите въз основа на вероятността и сериозността на повредата. Режимът на повреда се отнася до всякакви дефекти или грешки в дизайн, процес или артикул, които засягат клиента. „Анализ на ефектите“се отнася до изследването на последствията от неуспехите.
Какво е PFMEA?
PFMEA означава анализ на ефектите на режима на повреда на процеса. Тази методология може да идентифицира потенциални режими на отказ в процеси на ниво операции. Като цяло екип с технически опит провежда PFMEA. Основният процес е събиране на подходящи данни за причините за режимите на повреда, за да се коригират или минимизират ефектите от режима на повреда.
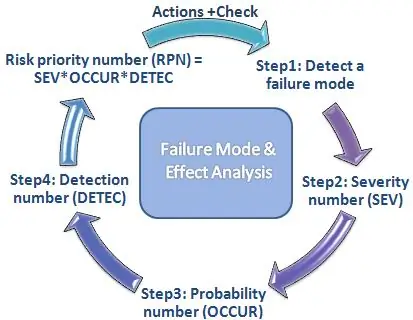
Освен това, PFMEA е структуриран инструмент, използван от всички видове организации. Той помага при изграждането на въздействията на режимите на повреда и приоритизира действията, необходими за облекчаване на риска. PFMEA се документира и представя преди стартирането на нови процеси за намаляване на потенциалните опасности. Освен това е възможно да се приложи това към преобладаващи процеси, за да се постигне непрекъснато подобряване на системата.
Какво е DFMEA?
DFMEA означава анализ на ефектите на режима на грешка при проектиране. Тази методология помага да се идентифицират потенциални грешки в дизайна на продукта на етапа на разработка. В повечето случаи инженерите използват това като процедура за изследване на възможността за неизправност на дизайна в реална ситуация или употреба.
Основният инженерен инструмент за DFMEA е DFMEA матрица. Тази матрица представя структура за компилиране и документиране на свързана информация, включително технически спецификации, дати на издаване, дати на преразглеждане и членове на екипа. Като цяло DFMEA е екипна работа от технически опит и вероятно многофункционален екип. Освен това DFMEA не разчита на контроли на процеси за преодоляване на възможни грешки в дизайна
Какви са приликите между PFMEA и DFMEA?
- PFMEA и DFMEA са два вида анализ на ефектите на режим на повреда.
- Основните стъпки в DFMEA и PFMEA са подобни, но имат две различни приложения.
- Както DFMEA, така и PFMEA показват възможни повреди, сериозността на рисковете, съществуващи контроли, препоръки и подобрения след препоръчани действия.
- Крайната цел и на двете е да се намалят или избегнат големи пропуски на продукти и производство.
- Тези методологии също могат да намалят разходите за проектиране или експлоатация.
- Освен това, някои повреди може да не бъдат смекчени в DFMEA. Тези грешки могат да бъдат прехвърлени към PFMEA за предприемане на необходимите контроли за подобряване на продукта.
Каква е разликата между PFMEA и DFMEA?
Основната разлика между PFMEA и DFMEA е, че PFMEA включва процеси, докато DFMEA включва продуктов дизайн. Основната цел на DFMEA е да разкрие потенциални неуспехи на продуктовия дизайн, докато основната цел на PFMEA е да разкрие потенциални неуспехи на процесите. Основният преглед на DFMEA се извършва с помощта на продуктова схема, докато PFMEA се провежда с помощта на диаграма на процеса. Друга разлика между PFMEA и DFMEA е, че PFMEA се случва на оперативно ниво, докато DFMEA се случва на етапа на разработка.
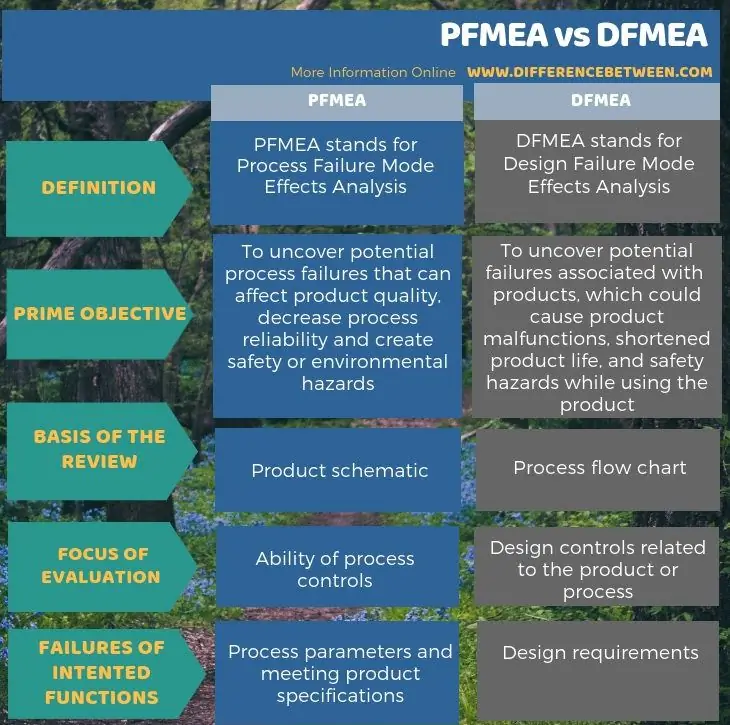
Обобщение- PFMEA срещу DFMEA
Ключовата разлика между PFMEA и DFMEA е, че PFMEA помага да се анализират потенциални неуспехи на определен процес на ниво работа, докато DFMEA помага да се анализират потенциални неуспехи на дизайн на продукта на ниво проектиране и разработка. Освен това тези методологии ще намалят производствените разходи, както и възможните неуспехи при пускането на продукти.